FAQ at Beska
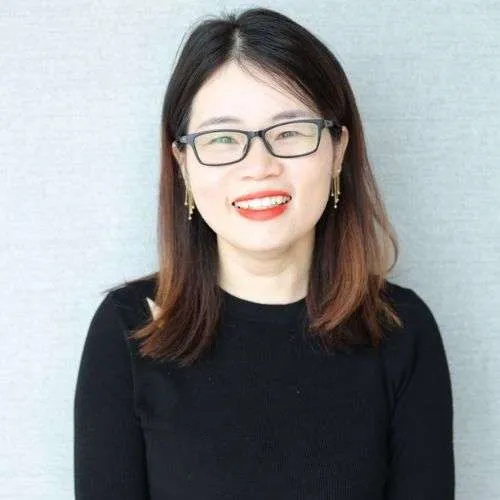
Beska – Best Quality with Competitive Price.
With expertise in sheet metal fabrication and CNC machining, we’re here.






Topics
General Questions
Beska is a custom prototyping and manufacturing service supplier in the USA. We are aimed at becoming your top-list manufacturing partner to bring your unique design into reality.
Â
At Beska, our capability covers CNC machining, 3D printing, vacuum casting, injection molding, sheet metal fabrication, and die casting. We are fully confident to serve you custom service from low-volume prototyping to mass production. Additionally, 90% of our staff have 10+ years’ experience. We combine the expertise and the advanced technologies to create high-performance components for you.
Â
The Beska team will keep improving our capability to create more possibilities for your potential project.
The industries that the Beska team has covered are automotive, aerospace, electronics, medical, robotics, agricultural, etc.
No, we only provide production services. If you need any engineering suggestions, we are fully capable of supporting you.
Yes, we can. NDA(Non-Disclosure Agreement) files play a role as the guarantee to protect your design work. As an experienced manufacturer, we are glad to sign the NDA files with you first to accelerate the partnership between us.
Beska’s capability covers CNC machining, 3D printing, vacuum casting, injection molding, sheet metal fabrication, and die casting. We are a custom manufacturer that is committed to offering high-quality components.
The common international deliveries at Beska include DHL, FedEx, UPS, and EMS. If you have other requirements for delivery, we will do that as long as we can.
It depends on your project. Small-volume prototyping usually gets done quickly, while larger-scale production like die casting and injection molding can take longer. For sheet metal fabrication prototypes, the lead time varies based on how complex the design is and the availability of materials. Generally, we can produce parts in a matter of days or weeks, depending on the scope of your project.
To create a successful product, we recommend starting with a rapid prototype of your design. We use CNC machining or vacuum casting to make these prototypes, which allows you to test your product and gather feedback. As you refine your design, we can easily scale up production to meet higher volumes. Our team supports you from the initial idea to the final product, delivering high-quality results at each step.
Questions During Quotation
At Beska, we can accept drawing formats in igs/x-t/step/stp.
As for prototyping projects on CNC machining and 3D printing, there is no minimum quantity at Beska. If you get any mass production projects including die casting and injection molding, our minimum quantity is around 1000 pieces and there is no maximum limit.
At Beska, there is a variety of material ranges to support your project. The plastic materials available are ABS, Nylon, PC, POM, PMMA, PEEK, and HDPE. The metal materials range includes aluminum, stainless steel, copper, brass, carbon steel, and zinc. Other rare materials include wood and glass.
The Beska team based our quotations on 4 aspects: 3D & 2D files, raw materials, manufacturing method, and quantity. After analyzing your files and calculating the general cost, we will give you a quote in a few hours.
Yes, we can give a rough quote according to your pictures. However, if you get the 3D & 2D files, the quotation will be more accurate.
Generally speaking, a prototyping project may take 2~4 hours. As for molding and die-casting projects, we may need a longer time to send the quotation to you.
Yes, we also offer assembling services to save you time and energy.
At Beska, there is a wide range of surface finishes to serve your production needs. It involves polishing & sanding, painting, anodizing, powder coating, passivation, electroplating, etc.
You can send your 2D files to us, and we will determine whether we can achieve the required tolerances. However, several factors may affect the tolerance range at Beska, including material, size, design, surface treatment, and the manufacturing method.
Â
CNC machining can achieve higher precision with tolerances of ±0.005mm. For sheet metal parts, we follow ISO 2768-mk standards to control their shapes and sizes. These standards cover a range of tolerances for linear and angular dimensions, flatness & straightness, cylindricity, and circularity.
In-process and After-sales Questions
Before production, we will conduct a comprehensive manufacturing design to point out issues that may affect the project. As for quality inspection, there are 4 steps to guarantee the quality of the parts: raw material inspection, in-process inspection, final quality check, and inspection equipment maintenance.
- Raw material inspection: All the raw materials will go through a series of tests.
- In-process: It relies on the collaboration between the manufacturing staff and the quality checking team. The quality checking team will do multiple checks on the parts to ensure the quality.
- Before shipment: This quality inspection will determine whether the part will be shipped. So we make a CMM quality inspection report and share it with you. In this way, if there are any problems in the process, you can give us feedback. And we can make adjustments in time.
- Equipment maintenance: The accuracy of quality checking equipment is pretty important.
Yes, we will send pictures and videos to send you updates on the latest processing of the project.
Yes, we provide complete machining guidance from material selection to custom packaging.
Our team always puts the quality of the parts first. All parts are made according to your machining requirements. If there are any problems with the process, our after-sales team will continue to solve the problem for you. If the quality problem is caused by us not making it according to your requirements, we can redo the parts for you until you’re satisfied
About Sheet Metal Fabrication
Sheet metal fabrication is a process that Beska uses to shape thin metal sheets into parts you might need, like enclosures, brackets, and chassis. This technique is great for making precise and durable items that work well in many different industries.
Â
At Beska, we specialize in sheet metal fabrication to provide you with top-quality and reliable products all the time. Our services are perfect for creating high-performance parts that meet your specific needs.
Sheet metal fabrication is ideal for both prototypes and large-scale production. At Beska, we use advanced technologies for high-precision cutting and forming, making sure your parts are made accurately.
- High Precision: Advanced technologies for accurate cutting and forming.
- Durability: Strong and long-lasting metal components suitable for tough environments.
- Cost-Effective: Efficient use of materials and adaptable to both small and large production runs.
- Finishing Techniques: Various options like powder coating for added protection and a polished look.
Sheet metal is incredibly versatile and can be used for many different purposes. At Beska, we fabricate a wide range of metal parts, including:
- Electrical enclosures
- Computer electronics parts
- Sturdy chassis
- Precise brackets
- Durable cabinets
Whether you need a lot of parts or just a few custom ones, we can handle them.
The K factor in sheet metal is the ratio of the neutral axis to the material thickness. This factor changes based on the physical properties and thickness of the materials we use. At Beska, we take the K factor into account to achieve accurate bends and shapes in your parts.
The cost of a sheet metal fabrication project includes several factors such as the design, prototype, finishing processes, and materials used. At Beska, we provide detailed quotes so you know exactly what to expect, helping you plan your budget effectively. For a customized quote and more information, please contact our team.
A prototype sheet metal fabricator specializes in making small quantities of custom-designed sheet metal parts. At Beska, we use various techniques to create prototypes that you can use for testing, experimentation, and evaluation.
We can use many different materials for sheet metal fabrication, including steel, stainless steel, aluminum, copper, and brass. The best material for your project depends on how you will use the part, its structural needs, and how you want it to look.
To find a reliable prototype sheet metal fabricator, research is key. Look for companies with experience in the type of fabrication you need. Check their references and past work examples. Also, consider their pricing, lead time, and customer service. At Beska, we pride ourselves on our expertise, transparency, and customer support.
About CNC Machining
CNC machining is a process where computer-controlled machines cut and shape materials like metal, plastic, and wood. We use this method to create prototypes and production parts for various industries, including automotive, aerospace, and medical.
CNC machining offers high precision and repeatability, making it ideal for creating intricate parts. Beska’s CNC machining can handle a variety of materials and provides fast production times and consistent quality, making it essential for modern manufacturing.
3D printing builds parts layer by layer, adding material to create the desired shape. CNC machining, on the other hand, starts with a solid block of material and removes sections to form the part. 3D printing is great for complex designs and rapid prototyping, while CNC machining is best for durability, precision, and material versatility.
In our CNC machining process, we often use both aluminum and stainless steel. Aluminum is lightweight and easy to machine, making it suitable for applications where weight is a factor. On the other hand, stainless steel is heavier but offers higher strength and corrosion resistance, making it ideal for more demanding environments.
At Beska, we use both 6061 and 7075 aluminum in our CNC machining. 6061 aluminum is versatile and easier to work with, offering good strength and corrosion resistance. 7075 aluminum is stronger and harder but can be more challenging to machine, often used in high-stress applications like aerospace.
Bronze is typically harder and more wear-resistant, making it suitable for heavy-duty applications. Brass is softer and easier to machine, often used for decorative parts and applications requiring good electrical conductivity.
Plastic CNC machining is a great choice for making parts because plastic parts are lightweight, easy to work with, and usually cheaper than metal parts. At Beska, we use CNC machining to create plastic parts that fit a wide range of needs, making it a favorite for engineers and product teams.
Thermoset plastic, once molded, cannot be melted and reshaped, making it ideal for parts that need to retain their shape. Thermoplastic, on the other hand, can be melted and reformed. It is often used in injection molding.
The best plastic for CNC machining depends on what you need the final product to do. Softer plastics are easier to machine but might not be as strong as harder plastics, which are necessary for more demanding applications. Here are some common plastics we use in our CNC machining but not limited to:
- Polyethylene (PE): Lightweight and durable.
- Polypropylene (PP): Resistant to chemicals and moisture.
- Acrylonitrile Butadiene Styrene (ABS): Strong and impact-resistant.
- Polycarbonate (PC): Very tough and transparent.
- Ultem (PEI): High strength and heat resistance.
About Metal Stamping
Metal stamping is a process we use to shape or cut unheated sheet metal using a tool and die mold or stamping press. Our stamping presses can perform various techniques like punching, embossing, bending, flanging, and coining to create the exact shapes you need.
Deep draw stamping is a technique we use to produce hollow metal components. At Beska, we achieve this by pulling and stretching the metal through a die with a cavity. The depth of the part is determined by how many times the metal is drawn through the die.
In progressive die stamping, we use a series of stamping dies to cut, punch, bend, or perform other operations on a single workpiece. At Beska, this process continues until the finished part exits the final station, allowing for efficient and consistent production.
At Beska, we use various metal fabrication techniques to create specific shapes from metal sheets, bars, or rods. These include:
- Extrusion: Forcing metal through a narrow die to produce a round tube cross-section.
- Forging: Shaping metal by striking it with force in a die or with a hammer.
- Machining: Cutting, drilling, carving, and other shaping operations to remove excess material.
- Milling: Using CNC equipment for precise, multiple-axis cutting.
- Turning: Rotating parts on a lathe while a stationary blade removes unwanted material.
- Punching: Striking metal to indent or perforate it according to specific designs.
- Welding: Connecting separate metal parts through heat and/or pressure.
Metal stamping offers several benefits including:
- Quick production times
- High precision in parts
- Uniform quality across parts
- Applicable to various designs and industries
- Efficient use of materials
- Cost-Effective
At Beska, we determine the best materials for metal stamping based on their characteristics and how well they can be stamped or machined. The function and performance requirements of the application are also considered. For example, office metal baskets might not need high-performance steel, while industrial kitchen counters require food-grade stainless steel. Here are some common materials we use:
- Ferrous Metals: Steel, stainless steel, carbon steel.
- Nonferrous Metals: Aluminum, brass, bronze, zinc.
- Custom Alloys: Beryllium copper, beryllium nickel.
- Precious Metals: Gold, silver, platinum.
At Beska, we choose the best metal stamping process based on achieving the desired results with the fewest steps, minimal scrap material, and cost-effectiveness. Reusing existing dies or utilizing progressive stamping for large production runs can save time and money in the long run.
About Galvanized and Galvannealed Steel
Galvanized steel is coated with a layer of zinc to protect it from rust and corrosion. On the other hand, galvannealed steel goes through an extra step called annealing after being galvanized, which forms a zinc-iron alloy. This makes it even more durable and resistant to corrosion. At Beska, we use both types of steel to match the specific needs of your project.
Think about where and how the steel will be used. Galvanized steel has a shiny finish, making it good for visible parts like solar panel mounts. Galvannealed steel has a duller finish and is more durable, making it better for internal parts that need to withstand tough conditions. Our team at Beska can help you decide which type is best suited for your project’s requirements.
Both types of steel can lose some of their corrosion resistance at the cut edges, making them prone to rust. At Beska, we suggest that welding these steels requires good ventilation because of the toxic fumes and needs to be done carefully to avoid sparking. Also, finding thicker plates of these steels can be difficult, which might increase costs and lead times.
To improve the corrosion resistance of galvanized or galvannealed steel, we can use cold-rolled steel and apply a zinc coating after fabrication. This additional coating helps protect the cut edges from rusting. While this process can increase the overall cost and lead time, it provides enhanced rust resistance, making your parts more durable and reliable.
Beauty Innovation Starts Here
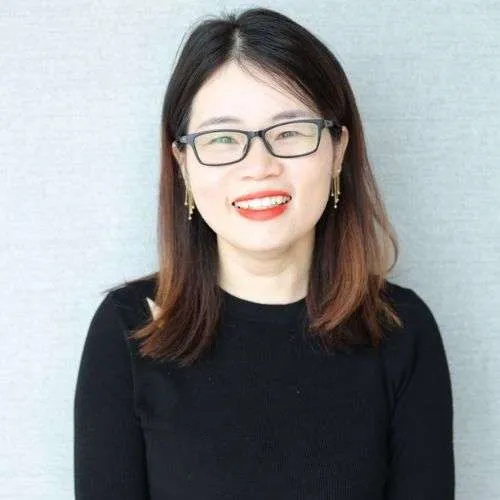
Beska – Best Quality with Competitive Price.
With expertise in sheet metal fabrication and CNC machining, we’re here.